
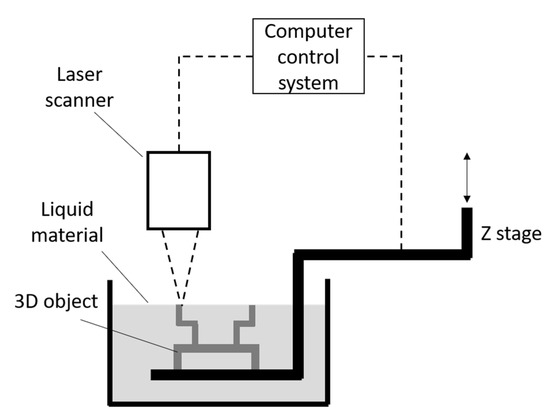
Many printers that use PDMS have a mechanism to assist the peeling of the part being printed from the PDMS, for example tilting or sliding of the vat after each layer exposure but some printers are able get by without any peel assist mechanism. PDMS has less “stickiness” when compared to FEP but is notorious for clouding after a relatively limited number of 3d prints leading to the need to replace the resin vat or at least the PDMS release layer of the vat often. Each material has advantages and disadvantages when used in 3d printing. Most “bottom up” dlp and sla resin based 3d printers use one of two materials as a release layer for peeling a part from the floor of the printers resin vat after a layer exposure, PDMS which is a type of transparent silicone or FEP which is a transparent Teflon.
#Creation workshop is slice thickness z full#
Full build details will be made available (dxf’s, stl’s wiring diagrams, marlin firmware settings etc.) once I freeze the design so stay tuned. I still have a bit over a month before the build presentation at the makerspace so with so much time still available some minor changes in the design are inevitable, I will also probably add an optional cover.

The Cool Breeze seems to fulfill all of the requirements I set for an inexpensive DIY 3d resin printer build. The vat platform can be raised and lowered as can the projector platform, the 45 degree mirror can be raised or lowered, moved forwards or backwards or removed if the printer is set up to use a lcd, the linear slide and carriage can also be adjusted up or down. I also wanted the printer to be able to be quickly and easily be built using the resources of any local makerspace or reasonably equipped workshop.Īnother important requirement was adjustability, I wanted every part of the printer to be adjustable since this would allow the builder to adapt the printer frame to any projector and vat size within reason or even use uv/daylight lcd’s for layer imaging if desired. My main goal was to create a printer that was inexpensive (printer frame and electronics $150.00-$175.00), that used readily available parts, materials and components.
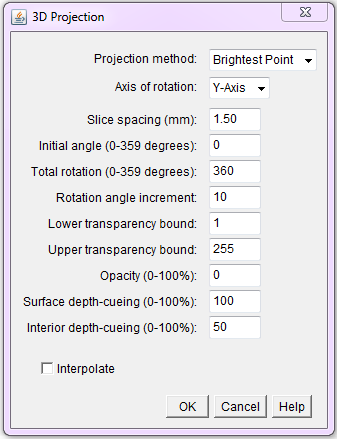
#Creation workshop is slice thickness z free#
Since then I started designing a printer in my free time, eventually made 2d and 3d CAD drawings which I then used to make the 3d prints and laser cut acrylic parts for the construction of the printer frame shown below. The machines I build can look pretty steampunk but apparently the presentation created some interest for building DIY resin printers at the makerspace. For the presentation I brought in the printer I built for printing high resolution master parts and vat testing (for my vats). A month or so ago I did a presentation at the local makerspace about dlp based 3d resin printers.
